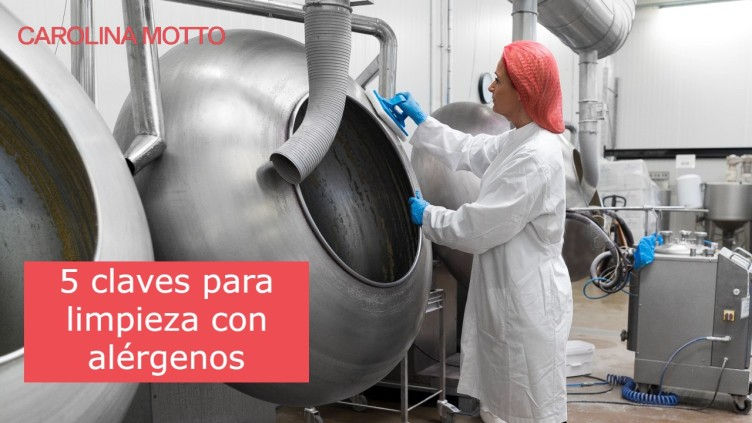
“Gliadina: Detectable” leyó Inés en el Asunto del correo.
De todas los fallos posibles, la presencia de gluten en el producto del lanzamiento era la tragedia máxima.
“Gliadina: Detectable”, repitió Inés mientras hilvanaba, como en un verso, los hechos y los datos que le permitieran dimensionar el problema:
10K unidades de producto
de “Edición Limitada”
que declaran “Libre de Gluten”
Para “ese Cliente-con-el-que-no-podemos-fallar”
Y que tienen que salir a ventas en 2 días según el Gantt de la innovación
“No puede ser, tiene que haber algún error”, pensó mientras llamaba a Mercedes, supervisora del laboratorio.
“Ya repetí el ensayo, amplié el muestreo y testeé el kit contra blanco. El resultado es correcto: Gliadina: detectable”, respondió Mercedes anticipándose a la pregunta y haciendo trizas la única esperanza de frenar la tormenta perfecta.
“Gracias” respondió Inés confirmando, por un lado, la proactividad de Mercedes (“sin dudas va a llegar muy lejos”) y por otro, el comienzo de una crisis.
“Es la primera vez que pasa esto”
“Si validamos la limpieza hace seis meses, ¿Qué puede haber pasado”?
“La semana pasada produjimos la misma referencia y dio gliadina negativo”
“Miré los registros y la limpieza se hizo correctamente. Incluso se verificó con el test de gliadina y dio negativo en todos los puntos que se hisoparon”
“El lanzamiento está pautado para dentro de 2 días: ¿tenemos plan B?
En la sala de reuniones todos hacían preguntas intentando, por un lado, ensayar una explicación posible y por otro, pensar formas de resolver el problema. El clima de tensión iba en aumento. Cada vez eran más los teléfonos que sonaban con pedidos de explicaciones.
Había que volver a producir, estaba claro, pero, como diría el número 1 de todos los tiempos, hacerlo en las mismas condiciones sólo podía garantizar el mismo resultado. O sea, “Gliadina: detectable”.
Inés reunió al equipo de inocuidad y a todos los operadores que habían participado de la producción problema.
En medio de la lluvia de ideas, Bruno, el operador de elaboración recordó que el día anterior se habían colocado unas tuberías nuevas para el envío de polvos por gravedad, desde la tolva de descarga de ingredientes del primer piso directamente al reactor. Esas nuevas tuberías, plásticas, reemplazaban las anteriores, de tela, que tardaban mucho tiempo en secarse después de la limpieza húmeda.
Las nuevas tuberías no se podían desmontar fácilmente como las anteriores y no se habían limpiado antes de comenzar a elaborar la “edición limitada”.
“No sabíamos cómo limpiarlas y no teníamos el instructivo; quedaron sin limpiar de la producción anterior”, dijo Bruno mientras sus compañeros asentían.
Cuando se descubre la causa raíz, suceden, por lo general, 4 cosas en el siguiente orden cronológico:
Alivio colectivo: Sensación de ver la luz al final del túnel compartida.
Intento de “desmarcarse” de la responsabilidad por lo ocurrido: “yo no sabía” “nadie me avisó” ¿Quién autorizó el cambio de tuberías?” ¿Cómo no volvimos a validar después del cambio? etc, etc, etc (aquí el lector puede sumar tantos etc como le plazca!)
Catarsis: “acá siempre pasa lo mismo”, “nadie comunica los cambios”, “así no se puede trabajar”
Acción: “en media hora en mi oficina para pensar los próximos pasos”
Y como lo mío es la acción, te cuento cómo resolvieron el problema en la planta de Inés (y, por supuesto, si lograron llegar a tiempo para el lanzamiento!)
El programa de limpieza validado para remover gluten, hasta el evento de contaminación, era el siguiente:

Desde la validación, el único cambio había sido el reemplazo de las tuberías de tela por otras plásticas, de difícil remoción. En este caso, no podía utilizarse limpieza húmeda porque no se podría garantizar el completo secado antes del uso (no hay mayor enemigo para el envío de polvos que una tubería mojada) ni tampoco limpieza en seco, porque no sería efectiva para remover el gluten.
Propusieron entonces un cambio:

Fast forward (fin de la historia):
Implementaron la nueva secuencia de lavado. Después de una corrida de prueba y todas las muestras con resultado negativo de gliadina, produjeron un nuevo lote de “Edición Limitada”.
Los primeros golpes de máquina fueron directo al laboratorio mientras todos esperaban, en vilo, la hora de la verdad.
Al rato, Inés recibió un correo. Esta vez el asunto rezaba: “Gliadina: no detectable”.
5 Tips para diseñar la estrategia para la limpieza de equipos y líneas compartidas:
La limpieza húmeda (CIP, COP o Manual) es la mejor opción, siempre que el proceso y la naturaleza del producto lo permitan. Esto es así porque la mayoría de las proteínas alérgénicas son solubles en agua.
Para la limpieza en seco, el uso de aspiradoras siempre es la mejor opción, siempre que resulte viable.
Para la limpieza por arrastre deben utilizarse materiales inertes no alergénicos (sal o almidón)
Cuando el agente de arrastre elegido no sea un ingrediente en el siguiente lote de producción, es necesario programar una limpieza posterior.
Siempre que resulte posible, es una buena alternativa que el material de arrastre sea utilizado como ingrediente en el próximo lote de producción que contenga el mismo perfil de alérgenos (por ejemplo, la sal utilizada para el arrastre luego de una producción de masa con huevo podría ser utilizada como ingrediente para una próxima producción de un alimento similar que contenga huevo). Cuando esto no resulte viable, el material de arrastre debe segregarse y disponerse de una forma tal que no pueda ocasionar contaminación por contacto cruzado.
¿Qué podés hacer hoy mismo para pasar a la acción?
Si sos líder de Calidad o consultor y querés diseñar tu programa de limpieza por alérgenos o mejorar el existente, te propongo:
En función de la complejidad alergénica de tu planta y de las premisas de diseño de tu programa de gestión de alérgenos, elaborá una matriz de limpieza. Te recomiendo confeccionar una matriz para los equipos de elaboración y otra para las líneas de envasado. Podés encontrar un ejemplo y más detalles en este artículo sobre "Política de Elaboración".
Identificá, en cada caso, el tipo de limpieza que mejor se adapta a tu proceso y que resulta efectiva para remover los alérgenos. Podés combinar los tres tipos de limpieza, como en la planta de Inés, para hacer más eficiente el proceso.
Diseñá el protocolo de validación con el método del peor escenario. Tenés una guía paso a paso en este artículo de "Validación del Programa de Limpieza".
Espero que esta información te aporte valor, que para mí significa que puedas mejorar tu día a día, que la puedas llevar a la práctica y te ayude a simplificar formas y procesos.
Que tengas un gran fin de semana!
Un abrazo,

Comments